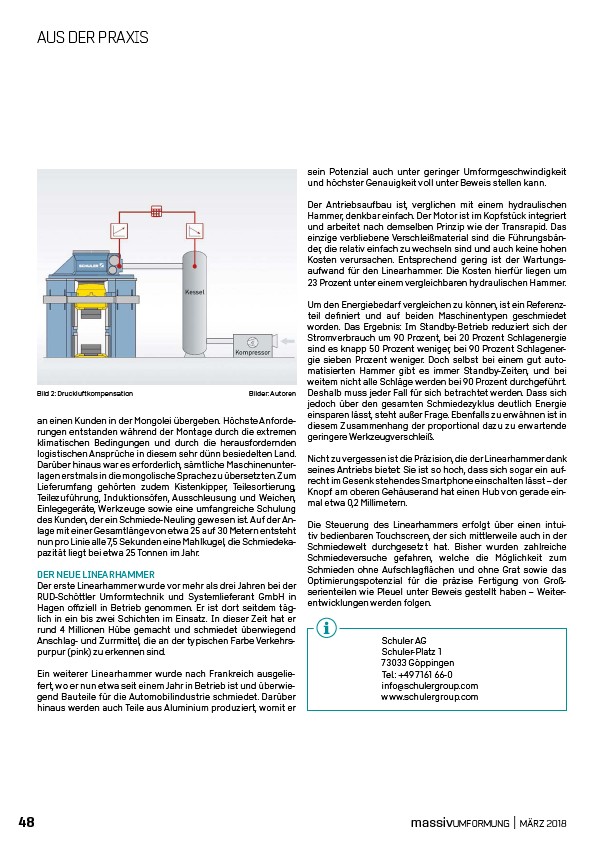
AUS DER PRAXIS
Bild 2: Druckluftkompensation Bilder: Autoren
an einen Kunden
in der Mongolei
übergeben.
Höchste Anforderungen
entstanden
während der Montage
durch die extremen
klimatischen
Bedingungen
und durch die herausfordernden
logistischen
Ansprüche
in diesem sehr dünn besiedelten
Land.
Darüber hinaus war es erforderlich,
sämtliche
Maschinenunterlagen
erstmals in die mongolische Sprache zu übersetzten. Zum
Lieferumfang
gehörten
zudem
Kistenkipper,
Teilesortierung,
Teilezuführung,
Induktionsöfen,
Ausschleusung
und Weichen,
Einlegegeräte,
Werkzeuge
sowie
eine umfangreiche
Schulung
des Kunden,
der ein Schmiede
Neuling
gewesen
ist. Auf der Anlage
mit einer Gesamtlänge
von etwa 25 auf 30 Metern entsteht
nun pro Linie alle 7,5 Sekunden
eine Mahlkugel,
die Schmiedekapazität
liegt bei etwa 25 Tonnen
im Jahr.
DER NEUE LINEARHAMMER
Der erste Linearhammer
wurde
vor mehr als drei Jahren
bei der
RUD-Schöttler
Umformtechnik
und Systemlieferant
GmbH in
Hagen
offiziell
in Betrieb
genommen.
Er ist dort seitdem
täglich
in ein bis zwei Schichten
im Einsatz.
In dieser
Zeit hat er
rund 4 Millionen
Hübe gemacht
und schmiedet
überwiegend
Anschlag
und Zurrmittel,
die an der typischen
Farbe Verkehrspurpur
(pink) zu erkennen
sind.
Ein weiterer
Linearhammer
wurde
nach Frankreich
ausgeliefert,
wo er nun etwa seit einem Jahr in Betrieb
ist und überwiegend
Bauteile
für die Automobilindustrie
schmiedet.
Darüber
hinaus
werden
auch Teile aus Aluminium
produziert,
womit
er
sein Potenzial
auch unter geringer
Umformgeschwindigkeit
und höchster
Genauigkeit
voll unter Beweis
stellen
kann.
Der Antriebsaufbau
ist, verglichen
mit einem hydraulischen
Hammer,
denkbar
einfach.
Der Motor
ist im Kopfstück
integriert
und arbeitet
nach demselben
Prinzip
wie der Transrapid.
Das
einzige
verbliebene
Verschleißmaterial
sind die Führungsbänder,
die relativ
einfach
zu wechseln
sind und auch keine hohen
Kosten
verursachen.
Entsprechend
gering
ist der Wartungsaufwand
für den Linearhammer:
Die Kosten
hierfür
liegen
um
23 Prozent
unter einem vergleichbaren
hydraulischen
Hammer.
Um den Energiebedarf
vergleichen
zu können,
ist ein Referenzteil
definiert
und auf beiden
Maschinentypen
geschmiedet
worden.
Das Ergebnis:
Im Standby
Betrieb
reduziert
sich der
Stromverbrauch
um 90 Prozent,
bei 20 Prozent
Schlagenergie
sind es knapp 50 Prozent
weniger,
bei 90 Prozent
Schlagenergie
sieben
Prozent
weniger.
Doch selbst bei einem gut automatisierten
Hammer
gibt es immer Standby
Zeiten,
und bei
weitem
nicht alle Schläge werden
bei 90 Prozent
durchgeführt.
Deshalb
muss jeder
Fall für sich betrachtet
werden.
Dass sich
jedoch
über den gesamten
Schmiedezyklus
deutlich
Energie
einsparen
lässt, steht außer
Frage.
Ebenfalls zu erwähnen ist in
diesem Zusammenhang der proportional dazu zu erwartende
geringere Werkzeugverschleiß.
Nicht zu vergessen
ist die Präzision,
die der Linearhammer
dank
seines
Antriebs
bietet:
Sie ist so hoch, dass sich sogar
ein aufrecht
im Gesenk
stehendes
Smartphone
einschalten
lässt – der
Knopf am oberen
Gehäuserand
hat einen Hub von gerade
einmal
etwa 0,2 Millimetern.
Die Steuerung
des Linearhammers
erfolgt
über einen intuitiv
bedienbaren
Touchscreen,
der sich mittlerweile
auch in der
Schmiedewelt
durchgesetzt
hat. Bisher
wurden
zahlreiche
Schmiedeversuche
gefahren,
welche
die Möglichkeit
zum
Schmieden
ohne Aufschlagflächen
und ohne Grat sowie
das
Optimierungspotenzial
für die präzise
Fertigung
von Großserienteilen
wie Pleuel unter Beweis
gestellt
haben
– Weiterentwicklungen
werden
folgen.
Schuler AG
Schuler-Platz 1
73033 Göppingen
Tel.: +49 7161 66-0
info@schulergroup.com
www.schulergroup.com
48 massivUMFORMUNG | MÄRZ 2018