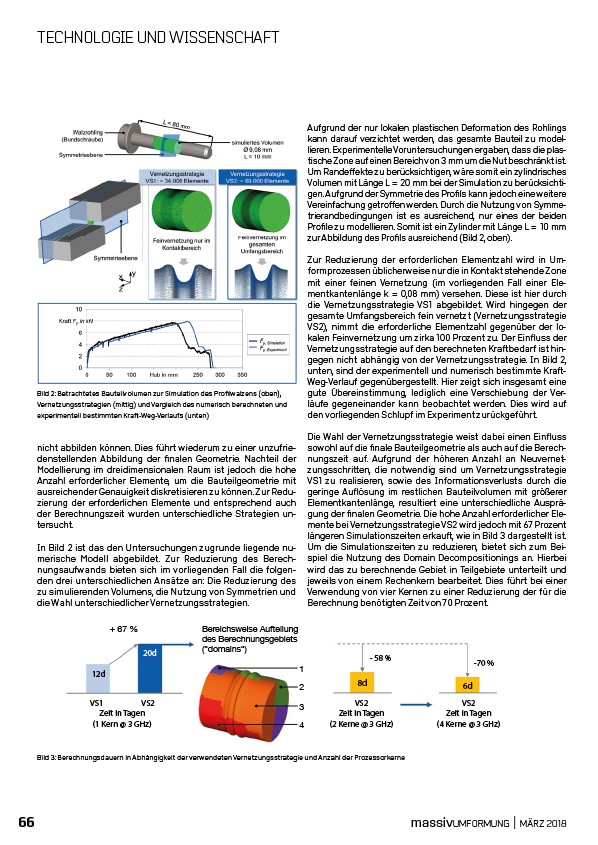
TECHNOLOGIE UND WISSENSCHAFT
Bild 2: Betrachtetes Bauteilvolumen zur Simulation des Profilwalzens (oben),
Vernetzungsstrategien (mittig) und Vergleich des numerisch berechneten und
experimentell bestimmten Kraft-Weg-Verlaufs (unten)
nicht abbilden
können.
Dies führt wiederum
zu einer unzufriedenstellenden
Abbildung
der finalen
Geometrie.
Nachteil
der
Modellierung
im dreidimensionalen
Raum ist jedoch
die hohe
Anzahl
erforderlicher
Elemente,
um die Bauteilgeometrie
mit
ausreichender
Genauigkeit
diskretisieren
zu können.
Zur Reduzierung
der erforderlichen
Elemente
und entsprechend
auch
der Berechnungszeit
wurden
unterschiedliche
Strategien
untersucht.
In Bild 2 ist das den Untersuchungen
zugrunde liegende
numerische
Modell
abgebildet.
Zur Reduzierung
des Berechnungsaufwands
bieten
sich im vorliegenden
Fall die folgenden
drei unterschiedlichen
Ansätze
an: Die Reduzierung
des
zu simulierenden
Volumens,
die Nutzung
von Symmetrien
und
die Wahl unterschiedlicher
Vernetzungsstrategien.
Aufgrund
der nur lokalen
plastischen
Deformation
des Rohlings
kann darauf
verzichtet
werden,
das gesamte
Bauteil
zu modellieren.
Experimentelle
Voruntersuchungen
ergaben,
dass die plastische
Zone auf einen Bereich
von 3 mm um die Nut beschränkt
ist.
Um Randeffekte
zu berücksichtigen,
wäre somit
ein zylindrisches
Volumen
mit Länge L = 20 mm bei der Simulation
zu berücksichtigen.
Aufgrund
der Symmetrie
des Profils
kann jedoch
eine weitere
Vereinfachung
getroffen
werden.
Durch die Nutzung
von Symmetrierandbedingungen
ist es ausreichend,
nur eines der beiden
Profile
zu modellieren.
Somit
ist ein Zylinder
mit Länge L = 10 mm
zur Abbildung
des Profils
ausreichend
(Bild 2, oben).
Zur Reduzierung
der erforderlichen
Elementzahl
wird in Umformprozessen
üblicherweise
nur die in Kontakt
stehende
Zone
mit einer feinen
Vernetzung
(im vorliegenden
Fall einer Elementkantenlänge
k = 0,08 mm) versehen.
Diese
ist hier durch
die Vernetzungsstrategie
VS1 abgebildet.
Wird hingegen
der
gesamte
Umfangsbereich
fein vernetzt
(Vernetzungsstrategie
VS2), nimmt die erforderliche
Elementzahl
gegenüber
der lokalen
Feinvernetzung
um zirka
100 Prozent
zu. Der Einfluss
der
Vernetzungsstrategie
auf den berechneten
Kraftbedarf
ist hingegen
nicht abhängig
von der Vernetzungsstrategie.
In Bild 2,
unten, sind der experimentell
und numerisch
bestimmte
Kraft-
Weg-Verlauf
gegenübergestellt.
Hier zeigt sich insgesamt
eine
gute Übereinstimmung,
lediglich
eine Verschiebung
der Verläufe
gegeneinander
kann beobachtet
werden.
Dies wird auf
den vorliegenden
Schlupf im Experiment
zurückgeführt.
Die Wahl der Vernetzungsstrategie
weist dabei
einen Einfluss
sowohl auf die finale
Bauteilgeometrie
als auch auf die Berechnungszeit
auf. Aufgrund
der höheren
Anzahl
an Neuvernetzungsschritten,
die notwendig
sind um Vernetzungsstrategie
VS1 zu realisieren,
sowie des Informationsverlusts
durch die
geringe
Auflösung
im restlichen
Bauteilvolumen
mit größerer
Elementkantenlänge,
resultiert
eine unterschiedliche
Ausprägung
der finalen
Geometrie.
Die hohe Anzahl
erforderlicher
Elemente
bei Vernetzungsstrategie
VS2 wird jedoch
mit 67 Prozent
längeren
Simulationszeiten
erkauft,
wie in Bild 3 dargestellt
ist.
Um die Simulationszeiten
zu reduzieren,
bietet
sich zum Beispiel
die Nutzung
des Domain
Decompositionings
an. Hierbei
wird das zu berechnende
Gebiet
in Teilgebiete
unterteilt
und
jeweils
von einem Rechenkern
bearbeitet.
Dies führt bei einer
Verwendung
von vier Kernen
zu einer Reduzierung
der für die
Berechnung
benötigten Zeit von 70 Prozent.
+ 67 % Bereichsweise Aufteilung
des Berechnungsgebiets
(“domains“)
-70 %
8d 6d
VS2
- 58 %
Zeit in Tagen
(2 Kerne @ 3 GHz)
VS2
Zeit in Tagen
(4 Kerne @ 3 GHz)
12d
20d
VS1 VS2
Zeit in Tagen
(1 Kern @ 3 GHz)
1
2
3
4
Bild 3: Berechnungsdauern in Abhängigkeit der verwendeten Vernetzungsstrategie und Anzahl der Prozessorkerne
66 massivUMFORMUNG | MÄRZ 2018