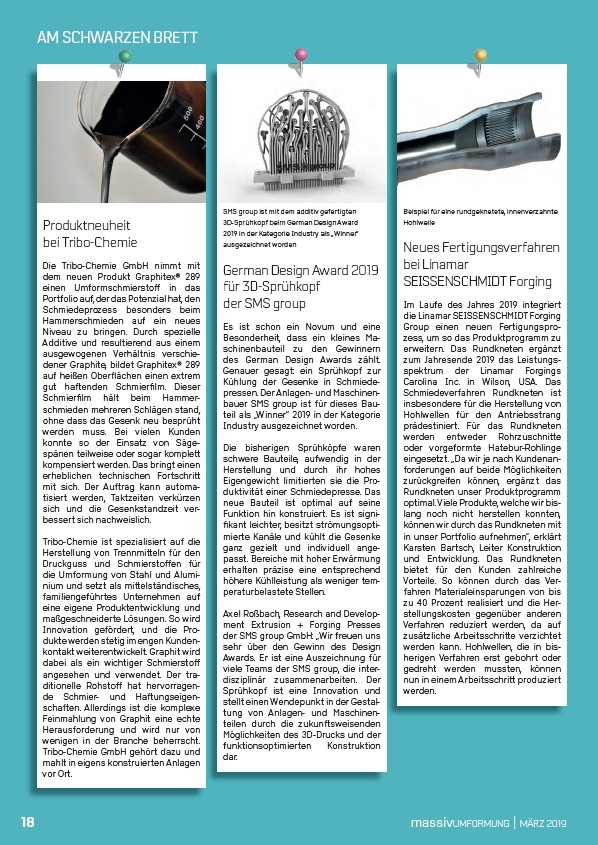
AM SCHWARZEN BRETT
Produktneuheit
bei Tribo-Chemie
Die Tribo-Chemie GmbH nimmt mit
dem neuen Produkt
Graphitex® 289
einen Umformschmierstoff
in das
Portfolio
auf, der das Potenzial
hat, den
Schmiedeprozess
besonders
beim
Hammerschmieden
auf ein neues
Niveau zu bringen.
Durch spezielle
Additive
und resultierend
aus einem
ausgewogenen
Verhältnis
verschiedener
Graphite, bildet Graphitex® 289
auf heißen Oberflächen
einen extrem
gut haftenden
Schmierfilm.
Dieser
Schmierfilm
hält beim Hammerschmieden
mehreren
Schlägen stand,
ohne dass das Gesenk neu besprüht
werden
muss. Bei vielen Kunden
konnte so der Einsatz
von Sägespänen
teilweise
oder sogar komplett
kompensiert
werden.
Das bringt einen
erheblichen
technischen
Fortschritt
mit sich. Der Auftrag
kann automatisiert
werden, Taktzeiten
verkürzen
sich und die Gesenkstandzeit
verbessert
sich nachweislich.
Tribo-Chemie ist spezialisiert
auf die
Herstellung
von Trennmitteln
für den
Druckguss
und Schmierstoffen
für
die Umformung
von Stahl und Aluminium
und setzt als mittelständisches,
familiengeführtes
Unternehmen
auf
eine eigene Produktentwicklung
und
maßgeschneiderte
Lösungen. So wird
Innovation
gefördert,
und die Produkte
werden
stetig im engen Kundenkontakt
weiterentwickelt.
Graphit wird
dabei als ein wichtiger
Schmierstoff
angesehen
und verwendet.
Der traditionelle
Rohstoff
hat hervorragende
Schmier- und Haftungseigenschaften.
Allerdings
ist die komplexe
Feinmahlung
von Graphit eine echte
Herausforderung
und wird nur von
wenigen
in der Branche
beherrscht.
Tribo-Chemie GmbH gehört dazu und
mahlt in eigens konstruierten Anlagen
vor Ort.
SMS group ist mit dem additiv gefertigten
3D-Sprühkopf beim German Design Award
2019 in der Kategorie Industry als „Winner“
ausgezeichnet worden
German Design Award 2019
für 3D-Sprühkopf
der SMS group
Es ist schon ein Novum und eine
Besonderheit,
dass ein kleines Maschinenbauteil
zu den Gewinnern
des German Design Awards zählt.
Genauer gesagt:
ein Sprühkopf
zur
Kühlung
der Gesenke
in Schmiedepressen.
Der Anlagen- und Maschinenbauer
SMS group ist für dieses Bauteil
als „Winner“ 2019 in der Kategorie
Industry ausgezeichnet
worden.
Die bisherigen
Sprühköpfe
waren
schwere Bauteile,
aufwendig
in der
Herstellung
und durch ihr hohes
Eigengewicht
limitierten
sie die Produktivität
einer Schmiedepresse.
Das
neue Bauteil
ist optimal
auf seine
Funktion
hin konstruiert.
Es ist signifikant
leichter, besitzt strömungsoptimierte
Kanäle und kühlt die Gesenke
ganz gezielt und individuell
angepasst.
Bereiche
mit hoher Erwärmung
erhalten
präzise
eine entsprechend
höhere Kühlleistung
als weniger
temperaturbelastete
Stellen.
Axel Roßbach, Research and Development
Extrusion + Forging Presses
der SMS group GmbH: „Wir freuen uns
sehr über den Gewinn des Design
Awards. Er ist eine Auszeichnung
für
viele Teams der SMS group, die interdisziplinär
zusammenarbeiten.
Der
Sprühkopf
ist eine Innovation
und
stellt einen Wendepunkt
in der Gestaltung
von Anlagen-
und Maschinenteilen
durch die zukunftsweisenden
Möglichkeiten
des 3D-Drucks und der
funktionsoptimierten
Konstruktion
dar.
Beispiel für eine rundgeknetete, innenverzahnte
Hohlwelle
Neues Fertigungsverfahren
bei Linamar
SEISSENSCHMIDT Forging
Im Laufe des Jahres 2019 integriert
die Linamar SEISSENSCHMIDT Forging
Group einen neuen Fertigungsprozess,
um so das Produktprogramm
zu
erweitern.
Das Rundkneten
ergänzt
zum Jahresende
2019 das Leistungsspektrum
der Linamar Forgings
Carolina Inc. in Wilson, USA. Das
Schmiedeverfahren
Rundkneten
ist
insbesondere
für die Herstellung
von
Hohlwellen
für den Antriebsstrang
prädestiniert.
Für das Rundkneten
werden entweder
Rohrzuschnitte
oder vorgeformte
Hatebur-Rohlinge
eingesetzt.
„Da wir je nach Kundenanforderungen
auf beide Möglichkeiten
zurückgreifen
können, ergänzt
das
Rundkneten
unser Produktprogramm
optimal.
Viele Produkte,
welche wir bislang
noch nicht herstellen
konnten,
können wir durch das Rundkneten
mit
in unser Portfolio
aufnehmen“,
erklärt
Karsten Bartsch, Leiter Konstruktion
und Entwicklung.
Das Rundkneten
bietet für den Kunden zahlreiche
Vorteile.
So können durch das Verfahren
Materialeinsparungen
von bis
zu 40 Prozent
realisiert
und die Herstellungskosten
gegenüber
anderen
Verfahren
reduziert
werden, da auf
zusätzliche
Arbeitsschritte
verzichtet
werden kann. Hohlwellen,
die in bisherigen
Verfahren
erst gebohrt
oder
gedreht
werden mussten, können
nun in einem Arbeitsschritt
produziert
werden.
18 massivUMFORMUNG | MÄRZ 2019