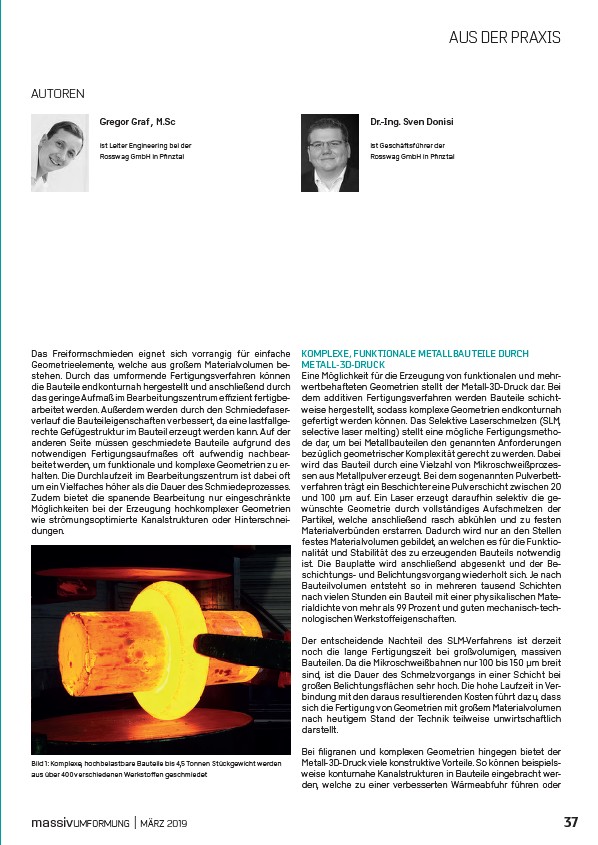
AUTOREN
Gregor Graf , M.Sc
ist Leiter Engineering bei der
Rosswag GmbH in Pfinztal
Das Freiformschmieden
eignet
sich vorrangig
für einfache
Geometrieelemente,
welche
aus großem
Materialvolumen
bestehen.
Durch das umformende
Fertigungsverfahren
können
die Bauteile
endkonturnah
hergestellt
und anschließend
durch
das geringe
Aufmaß
im Bearbeitungszentrum
effizient
fertigbearbeitet
werden.
Außerdem
werden
durch den Schmiedefaserverlauf
die Bauteileigenschaften
verbessert,
da eine lastfallgerechte
Gefügestruktur
im Bauteil
erzeugt
werden
kann. Auf der
anderen
Seite müssen
geschmiedete
Bauteile
aufgrund
des
notwendigen
Fertigungsaufmaßes
oft aufwendig
nachbearbeitet
werden,
um funktionale
und komplexe
Geometrien
zu erhalten.
Die Durchlaufzeit
im Bearbeitungszentrum
ist dabei
oft
um ein Vielfaches
höher als die Dauer des Schmiedeprozesses.
Zudem
bietet
die spanende
Bearbeitung
nur eingeschränkte
Möglichkeiten
bei der Erzeugung
hochkomplexer
Geometrien
wie strömungsoptimierte
Kanalstrukturen
oder Hinterschneidungen.
AUS DER PRAXIS
Dr.-Ing. Sven Donisi
ist Geschäftsführer
der
Rosswag GmbH in Pfinztal
Bild 1: Komplexe,
hochbelastbare
Bauteile
bis 4,5 Tonnen
Stückgewicht
werden
aus über 400 verschiedenen
Werkstoffen
geschmiedet
KOMPLEXE,
FUNKTIONALE
METALLBAUTEILE
DURCH
METALL-
3D-DRUCK
Eine Möglichkeit
für die Erzeugung
von funktionalen
und mehrwertbehafteten
Geometrien
stellt der Metall-
3D-Druck dar. Bei
dem additiven
Fertigungsverfahren
werden
Bauteile
schichtweise
hergestellt,
sodass
komplexe
Geometrien
endkonturnah
gefertigt
werden
können.
Das Selektive
Laserschmelzen
(SLM,
selective laser melting)
stellt eine mögliche
Fertigungsmethode
dar, um bei Metallbauteilen
den genannten
Anforderungen
bezüglich
geometrischer
Komplexität
gerecht
zu werden.
Dabei
wird das Bauteil
durch eine Vielzahl
von Mikroschweißprozessen
aus Metallpulver
erzeugt.
Bei dem sogenannten
Pulverbettverfahren
trägt ein Beschichter
eine Pulverschicht
zwischen
20
und 100 μm auf. Ein Laser
erzeugt
daraufhin
selektiv
die gewünschte
Geometrie
durch vollständiges
Aufschmelzen
der
Partikel,
welche
anschließend
rasch abkühlen
und zu festen
Materialverbünden
erstarren.
Dadurch
wird nur an den Stellen
festes
Materialvolumen
gebildet,
an welchen
es für die Funktionalität
und Stabilität
des zu erzeugenden
Bauteils
notwendig
ist. Die Bauplatte
wird anschließend
abgesenkt
und der Beschichtungs-
und Belichtungsvorgang
wiederholt
sich. Je nach
Bauteilvolumen
entsteht
so in mehreren
tausend
Schichten
nach vielen
Stunden
ein Bauteil
mit einer physikalischen
Materialdichte
von mehr als 99 Prozent
und guten mechanisch-
technologischen
Werkstoffeigenschaften.
Der entscheidende
Nachteil
des SLM-Verfahrens
ist derzeit
noch die lange Fertigungszeit
bei großvolumigen,
massiven
Bauteilen.
Da die Mikroschweißbahnen
nur 100 bis 150 μm breit
sind, ist die Dauer des Schmelzvorgangs
in einer Schicht bei
großen
Belichtungsflächen
sehr hoch. Die hohe Laufzeit
in Verbindung
mit den daraus
resultierenden
Kosten
führt dazu, dass
sich die Fertigung
von Geometrien
mit großem
Materialvolumen
nach heutigem
Stand der Technik
teilweise
unwirtschaftlich
darstellt.
Bei filigranen
und komplexen
Geometrien
hingegen
bietet
der
Metall-3D-Druck viele
konstruktive
Vorteile.
So können
beispielsweise
konturnahe
Kanalstrukturen
in Bauteile
eingebracht
werden,
welche
zu einer verbesserten
Wärmeabfuhr
führen
oder
massivUMFORMUNG | MÄRZ 2019 37