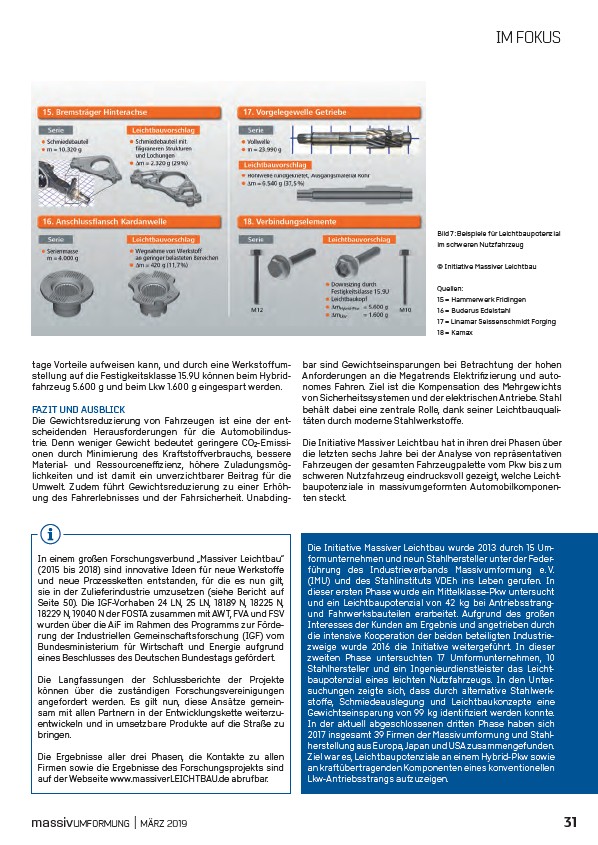
tage Vorteile
aufweisen
kann, und durch eine Werkstoffumstellung
auf die Festigkeitsklasse
15.9U können beim Hybridfahrzeug
5.600 g und beim Lkw 1.600 g eingespart
werden.
FAZIT UND AUSBLICK
Die Gewichtsreduzierung
von Fahrzeugen
ist eine der entscheidenden
Herausforderungen
für die Automobilindustrie.
Denn weniger Gewicht
bedeutet
geringere
CO2-Emissionen
durch Minimierung
des Kraftstoffverbrauchs,
bessere
Material- und Ressourceneffizienz,
höhere Zuladungsmöglichkeiten
und ist damit ein unverzichtbarer
Beitrag
für die
Umwelt. Zudem führt Gewichtsreduzierung
zu einer Erhöhung
des Fahrerlebnisses
und der Fahrsicherheit.
Unabdingbar
IM FOKUS
Bild 7: Beispiele für Leichtbaupotenzial
im schweren Nutzfahrzeug
© Initiative Massiver Leichtbau
Quellen:
15 = Hammerwerk
Fridingen
16 = Buderus
Edelstahl
17 = Linamar
Seissenschmidt
Forging
18 = Kamax
sind Gewichtseinsparungen
bei Betrachtung
der hohen
Anforderungen
an die Megatrends
Elektrifizierung
und autonomes
Fahren. Ziel ist die Kompensation
des Mehrgewichts
von Sicherheitssystemen
und der elektrischen
Antriebe. Stahl
behält dabei eine zentrale
Rolle, dank seiner Leichtbauqualitäten
durch moderne
Stahlwerkstoffe.
Die Initiative Massiver Leichtbau
hat in ihren drei Phasen über
die letzten sechs Jahre bei der Analyse
von repräsentativen
Fahrzeugen
der gesamten
Fahrzeugpalette
vom Pkw bis zum
schweren Nutzfahrzeug
eindrucksvoll
gezeigt,
welche Leichtbaupotenziale
in massivumgeformten
Automobilkomponenten
steckt.
In einem großen Forschungsverbund
„Massiver Leichtbau“
(2015 bis 2018) sind innovative Ideen für neue Werkstoffe
und neue Prozessketten
entstanden,
für die es nun gilt,
sie in der Zulieferindustrie
umzusetzen
(siehe Bericht auf
Seite 50). Die IGF-Vorhaben 24 LN, 25 LN, 18189 N, 18225 N,
18229 N, 19040 N der FOSTA zusammen mit AWT, FVA und FSV
wurden über die AiF im Rahmen des Programms
zur Förderung
der Industriellen Gemeinschaftsforschung
(IGF) vom
Bundesministerium
für Wirtschaft
und Energie
aufgrund
eines Beschlusses
des Deutschen Bundestags gefördert.
Die Langfassungen der Schlussberichte der Projekte
können über die zuständigen Forschungsvereinigungen
angefordert werden. Es gilt nun, diese Ansätze gemeinsam
mit allen Partnern
in der Entwicklungskette
weiterzuentwickeln
und in umsetzbare
Produkte
auf die Straße zu
bringen.
Die Ergebnisse
aller drei Phasen, die Kontakte
zu allen
Firmen sowie die Ergebnisse
des Forschungsprojekts
sind
auf der Webseite
www.massiverLEICHTBAU.de abrufbar.
Die Initiative Massiver Leichtbau wurde 2013 durch 15 Umformunternehmen
und neun Stahlhersteller
unter der Federführung
des Industrieverbands
Massivumformung
e. V.
(IMU) und des Stahlinstituts
VDEh ins Leben gerufen. In
dieser ersten Phase wurde ein Mittelklasse-
Pkw untersucht
und ein Leichtbaupotenzial
von 42 kg bei Antriebsstrang-
und Fahrwerksbauteilen
erarbeitet.
Aufgrund
des großen
Interesses
der Kunden am Ergebnis
und angetrieben
durch
die intensive
Kooperation der beiden beteiligten
Industriezweige
wurde 2016 die Initiative weitergeführt.
In dieser
zweiten Phase untersuchten
17 Umformunternehmen,
10
Stahlhersteller
und ein Ingenieurdienstleister
das Leichtbaupotenzial
eines leichten Nutzfahrzeugs.
In den Untersuchungen
zeigte sich, dass durch alternative
Stahlwerkstoffe,
Schmiedeauslegung
und Leichtbaukonzepte
eine
Gewichtseinsparung
von 99 kg identifiziert
werden konnte.
In der aktuell abgeschlossenen
dritten Phase haben sich
2017 insgesamt
39 Firmen der Massivumformung
und Stahlherstellung
aus Europa, Japan und USA zusammengefunden.
Ziel war es, Leichtbaupotenziale
an einem Hybrid-Pkw sowie
an kraftübertragenden
Komponenten
eines konventionellen
Lkw-Antriebsstrangs aufzuzeigen.
massivUMFORMUNG | MÄRZ 2019 31