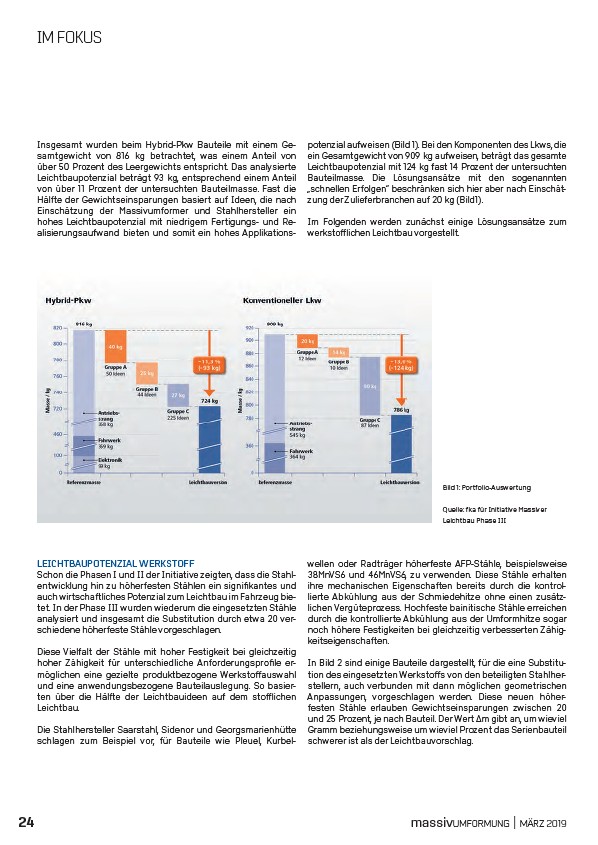
IM FOKUS
Insgesamt
wurden beim Hybrid-Pkw Bauteile
mit einem Gesamtgewicht
von 816 kg betrachtet,
was einem Anteil von
über 50 Prozent
des Leergewichts
entspricht.
Das analysierte
Leichtbaupotenzial
beträgt
93 kg, entsprechend
einem Anteil
von über 11 Prozent
der untersuchten
Bauteilmasse.
Fast die
Hälfte der Gewichtseinsparungen
basiert
auf Ideen, die nach
Einschätzung
der Massivumformer
und Stahlhersteller
ein
hohes
Leichtbaupotenzial
mit niedrigem Fertigungs-
und Realisierungsaufwand
bieten und somit ein hohes Applikationspotenzial
aufweisen
(Bild 1). Bei den Komponenten
des Lkws, die
ein Gesamtgewicht
von 909 kg aufweisen,
beträgt
das gesamte
Leichtbaupotenzial
mit 124 kg fast 14 Prozent
der untersuchten
Bauteilmasse.
Die Lösungsansätze
mit den sogenannten
„schnellen Erfolgen“
beschränken
sich hier aber nach Einschätzung
der Zulieferbranchen
auf 20 kg (Bild1).
Im Folgenden
werden zunächst einige Lösungsansätze
zum
werkstofflichen
Leichtbau
vorgestellt.
LEICHTBAUPOTENZIAL WERKSTOFF
Schon die Phasen I und II der Initiative zeigten, dass die Stahlentwicklung
hin zu höherfesten
Stählen ein signifikantes
und
auch wirtschaftliches
Potenzial
zum Leichtbau
im Fahrzeug
bietet.
In der Phase III wurden
wiederum
die eingesetzten
Stähle
analysiert
und insgesamt
die Substitution
durch etwa 20 verschiedene
höherfeste
Stähle vorgeschlagen.
Diese Vielfalt
der Stähle mit hoher Festigkeit
bei gleichzeitig
hoher Zähigkeit
für unterschiedliche
Anforderungsprofile
ermöglichen
eine gezielte
produktbezogene
Werkstoffauswahl
und eine anwendungsbezogene
Bauteilauslegung.
So basierten
über die Hälfte der Leichtbauideen
auf dem stofflichen
Leichtbau.
Die Stahlhersteller
Saarstahl, Sidenor und Georgsmarienhütte
schlagen zum Beispiel
vor, für Bauteile
wie Pleuel, Kurbelwellen
Bild 1: Portfolio-Auswertung
Quelle: fka für Initiative Massiver
Leichtbau Phase III
oder Radträger
höherfeste
AFP-Stähle, beispielsweise
38MnVS6 und 46MnVS6, zu verwenden.
Diese Stähle erhalten
ihre mechanischen
Eigenschaften
bereits
durch die kontrollierte
Abkühlung
aus der Schmiedehitze
ohne einen zusätzlichen
Vergüteprozess.
Hochfeste
bainitische
Stähle erreichen
durch die kontrollierte
Abkühlung
aus der Umformhitze
sogar
noch höhere Festigkeiten
bei gleichzeitig
verbesserten
Zähigkeitseigenschaften.
In Bild 2 sind einige Bauteile
dargestellt,
für die eine Substitution
des eingesetzten
Werkstoffs
von den beteiligten
Stahlherstellern,
auch verbunden
mit dann möglichen
geometrischen
Anpassungen,
vorgeschlagen
werden. Diese neuen höherfesten
Stähle erlauben
Gewichtseinsparungen
zwischen 20
und 25 Prozent,
je nach Bauteil.
Der Wert Δm gibt an, um wieviel
Gramm beziehungsweise
um wieviel
Prozent
das Serienbauteil
schwerer ist als der Leichtbauvorschlag.
24 massivUMFORMUNG | MÄRZ 2019