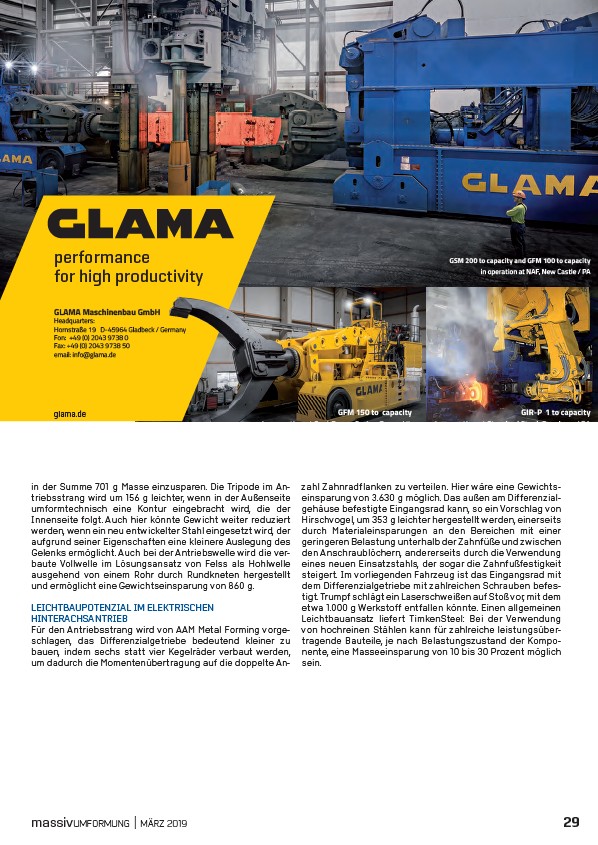
in operation at Scot Forge, Spring Grove / IL
performance
for high productivity
GLAMA Maschinenbau GmbH
Headquarters:
Hornstraße 19 D-45964 Gladbeck / Germany
Fon: +49 (0) 2043 9738 0
Fax: +49 (0) 2043 9738 50
email: info@glama.de
glama.de
in der Summe 701 g Masse einzusparen.
Die Tripode
im Antriebsstrang
wird um 156 g leichter, wenn in der Außenseite
umformtechnisch
eine Kontur
eingebracht
wird, die der
Innenseite
folgt. Auch hier könnte
Gewicht
weiter reduziert
werden, wenn ein neu entwickelter
Stahl eingesetzt
wird, der
aufgrund
seiner Eigenschaften
eine kleinere
Auslegung
des
Gelenks ermöglicht.
Auch bei der Antriebswelle
wird die verbaute
Vollwelle
im Lösungsansatz
von Felss als Hohlwelle
ausgehend
von einem Rohr durch Rundkneten
hergestellt
und ermöglicht
eine Gewichtseinsparung
von 860 g.
LEICHTBAUPOTENZIAL IM ELEKTRISCHEN
HINTERACHSANTRIEB
Für den Antriebsstrang
wird von AAM Metal Forming vorgeschlagen,
das Differenzialgetriebe
bedeutend
kleiner
zu
bauen, indem
sechs statt vier Kegelräder
verbaut
werden,
um dadurch
die Momentenübertragung
auf die doppelte
Anzahl
GSM 200 to capacity and GFM 100 to capacity
in operation at NAF, New Castle / PA
GFM 150 to capacity
GIR-P 1 to capacity
in operation at Standard Steel, Burnham / PA
Zahnradflanken
zu verteilen.
Hier wäre eine Gewichtseinsparung
von 3.630 g möglich.
Das außen am Differenzialgehäuse
befestigte
Eingangsrad
kann, so ein Vorschlag
von
Hirschvogel,
um 353 g leichter hergestellt
werden,
einerseits
durch Materialeinsparungen
an den Bereichen mit einer
geringeren
Belastung
unterhalb
der Zahnfüße
und zwischen
den Anschraublöchern,
andererseits
durch die Verwendung
eines neuen Einsatzstahls,
der sogar die Zahnfußfestigkeit
steigert.
Im vorliegenden
Fahrzeug
ist das Eingangsrad
mit
dem Differenzialgetriebe
mit zahlreichen
Schrauben
befestigt.
Trumpf schlägt ein Laserschweißen
auf Stoß vor, mit dem
etwa 1.000 g Werkstoff
entfallen
könnte. Einen allgemeinen
Leichtbauansatz
liefert TimkenSteel: Bei der Verwendung
von hochreinen
Stählen kann für zahlreiche
leistungsübertragende
Bauteile,
je nach Belastungszustand
der Komponente,
eine Masseeinsparung
von 10 bis 30 Prozent
möglich
sein.
massivUMFORMUNG | MÄRZ 2019 29